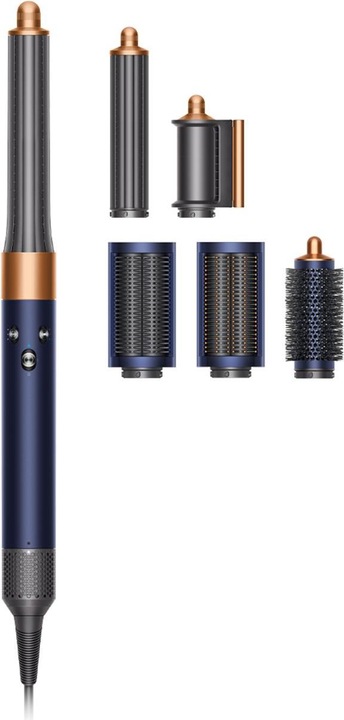
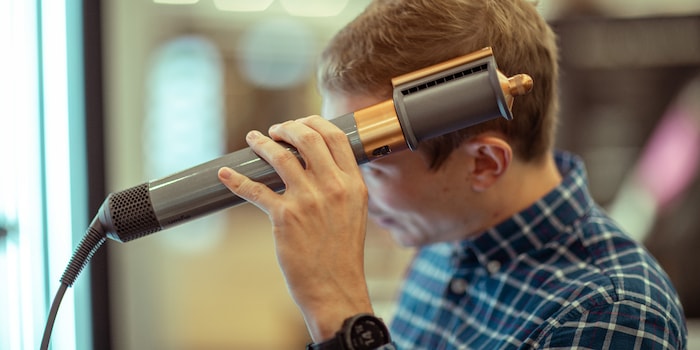
10 questions for Dyson engineer Ayrton Peel

What’s new for us is old hat for him. Ayrton Peel is part of Dyson’s engineering team, which developed the new Airwrap attachments. But what he’s working on now is a secret. In this interview, he lets me in on one or two things from his average work day.
Ayrton Peel is an engineer at Dyson. But not here in Switzerland. Instead, he works in Malmesbury in the UK. That’s where he’s been collaborating with his team on new and improved attachments for the Airwrap multi-styler. So, in a roundabout way, he’s partly responsible for making a hole in my wallet. Because after all, I simply must get my hands on anything Dyson Hair launches sooner or later. During his brief visit to Zurich, I met the 29-year-old engineer for a chat in the Dyson styling pop-up at Sihlcity.
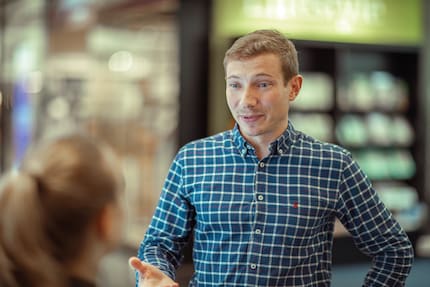
Source: Christian Walker
So, Ayrton, we have you to thank for improvements to Airwrap attachments. To what extent were you involved?
Ayrton Peel, New Product Innovation Engineer at Dyson: My team and I take part from the very beginning of every design process. We develop new ideas and concepts and try to improve existing products, such as the Airwrap. This involves drafting designs that we later use as the basis for our prototypes. At first, it’s just purely tinkering around. We cut things out and glue them by hand using cardboard boxes, for example. We only get stuck into computer modelling and 3D printing when we have a hunch that something could really work. That’s when the prototypes appear. Then you’ve got all the tests.

Source: Christian Walker
I’ve already heard a lot about your test labs. What exactly happens there?
We have various test laboratories. In performance testing, we work with devices that inspect our designs according to different requirements. For instance, we measure things like drying time with various attachments. We also dampen real strands of the most diverse hair types you can think of, and then we style them. By comparing before and after photos, we can establish how much we’ve improved styling capabilities. What’s more, our software developers have written computer programmes especially for our tests. These analyse images and count the number of flyaways. Or, they measure how straight the hair is. In other labs, we test how loud or robust the products are and if the controls still work after being used thousands of times.

Source: Christian Walker
You focussed in particular on the new Flyaway attachment. Where did the idea come from?
This innovation was born out of a specific problem that we kept having on campaign shoots for the Dyson Supersonic. The models’ hair was frizzy and damaged as a result of constant heat styling. My senior manager then noticed how the stylist on set solved the problem with a special hair drying technique and a round brush. We tried to transpose this principle into an attachment so that everyone could get the same effect on their own at home. After several attempts, we then found a way. At first, we couldn’t even believe how well it worked and more importantly, why it did.
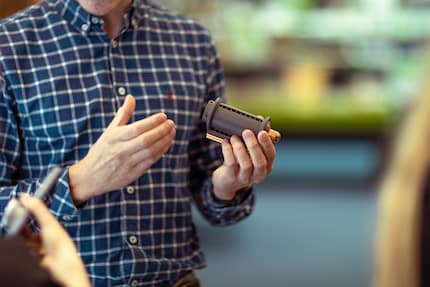
Source: Christian Walker
Then what?
We took slow-motion videos to see where the flyaways actually went. We also have so-called flow visualisation tools. These are devices that work with smoke. That way, we can see where exactly the air flows through. Upon completing these tests, we understood that broken, little short hairs were «hiding» under long ones. This flyaway technology was originally designed for the Airwrap. But as you can see, we first launched it as an attachment for the Supersonic, as it was easier to implement the concept there.
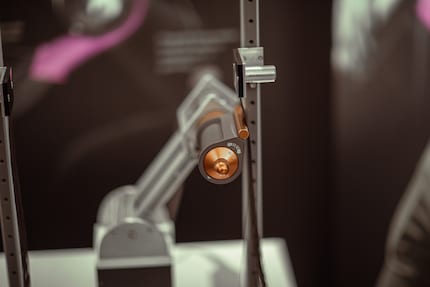
Source: Christian Walker
We’ve now covered a lot about the drying attachment. What’s something that a lot of people don’t know about your curling attachments?
The openings that the air emerges from along the shaft are exactly 0.5 mm wide. A lot of air gets blown through these. If the openings were even just a hundred micrometres bigger or smaller – about the thickness of a human hair – that would have a negative impact on air flow performance. It wasn’t just that we had to find the sweet spot; we also had to set up the manufacturing process so that we could ensure this precision with each individual attachment.

Source: Christian Walker
On the subject of hot air, when does it get too hot and start to damage your hair?
Starting at 150 degrees Celsius, the heat destroys alpha-carotene proteins.
Does that apply to all hair types?
Yes. All hair is made up of the same molecules. What differentiates them and determines the shape, type and structure of hair is the way the molecules are structured. You probably imagine that a cross section of hair is round. But that’s only the case with straight hair. The curlier the hair, the more a cross section will resemble a kidney bean. What’s more, the diameter of a strand changes depending on hair type. However, the actual protein structure is the same across all types of hair. And it gets damaged once it’s subjected to 150 degrees Celsius and above. That’s also why our Airflow products don’t exceed this. In fact, the Airwrap upper limit is actually 110 degrees Celsius.
What was the biggest challenge when developing a device like the Airwrap?
That we’re developing numerous attachments that all have to be ready at the same time for a set launch date. Initially, one or two engineers worked on each attachment. But the further we got into the development process, the more engineers we needed on board. Akin to the snowball principle. My team gave its designs to the next team, which was made up of three to five people. They then in turn handed their designs on to an even bigger team. There’s also the fact that not all the teams work in the same place. The initial process took place in Malmesbury in the UK. Meanwhile, our offices in Singapore are responsible for the final part of the manufacturing process. When it comes to projects that have to be implemented quickly, the time difference works in our favour. For instance, when we’re all clocking off, our colleagues in Singapore are just getting to work, and vice-versa. That was the case with the Flyaway attachment for the Supersonic. We developed and launched it in a very short space of time.
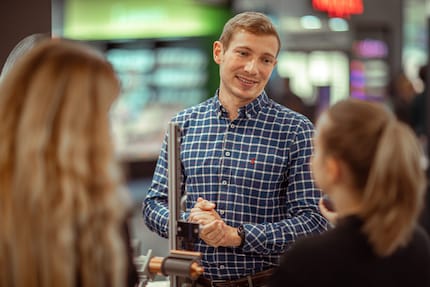
Source: Christian Walker
Will there be a third new and improved version of the attachments or does this draw a line under the Airwrap project?
My department is always coming up with new ideas. So, I can’t imagine we’ll ever stop improving current products. What I find fascinating is that I’m talking to you today about new attachments that were part of a project I stopped working on almost two years ago. The devices we’re launching right now are in the past when it comes to my timeline. I’ve developed other things in the meantime. Some of our engineers are working on projects that won’t be released for another ten years. That’s what makes it even nicer to see that people consider our developments new and exciting.
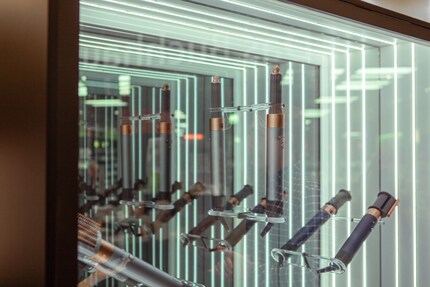
Source: Christian Walker
One last question I’m dying to know the answer to: what’s your favourite Airwrap colourway?
Dark blue and copper. The popular fuchsia isn’t my cup of tea, but hey, everyone is entitled to their own opinion (laughs).
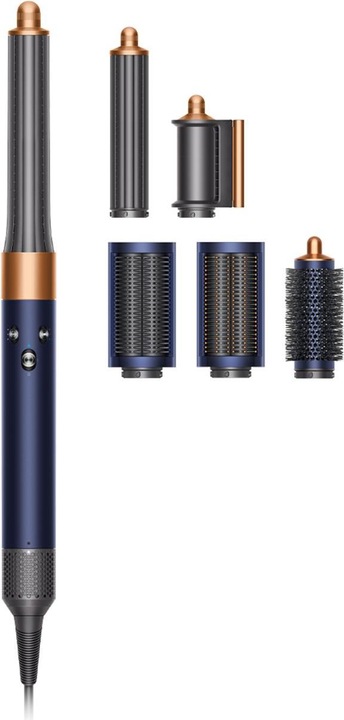
In the short-form feature «10 Questions for ...» I interview interesting people about their expertise, their passion or their lifestyle. Different people, different topics.


As a massive Disney fan, I see the world through rose-tinted glasses. I worship series from the 90s and consider mermaids a religion. When I’m not dancing in glitter rain, I’m either hanging out at pyjama parties or sitting at my make-up table. P.S. I love you, bacon, garlic and onions.